ELECTROSTATIC POWDER COATING FACILITY
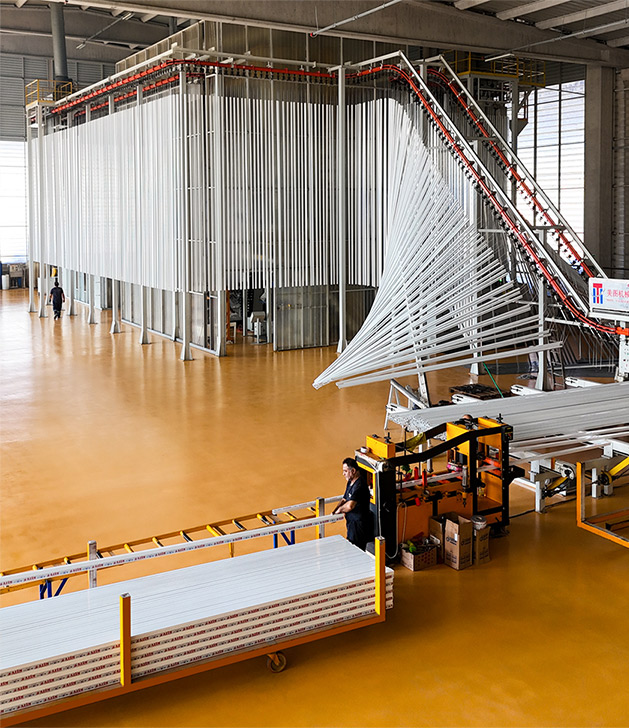
An electrostatic powder coating facility is a unit where aluminum profiles and surfaces are coated for protective and aesthetic purposes. The electrostatic powder coating process is carried out by electrically charging the powder paint and applying it to the aluminum surfaces. Initially, the paint adheres to the surface through electrostatic attraction, and then it is cured in an oven to harden. This method provides high durability while offering an environmentally friendly and aesthetically pleasing coating solution.
Properties of Electrostatic Powder Coating
Aluminum electrostatic powder coating facilities are particularly preferred in sectors where durability, aesthetics, and environmental factors are of significant importance. Electrostatic powder coatings enhance the resistance of aluminum profiles against scratches and wear. This technique effectively prevents the oxidation and rusting of aluminum surfaces, providing robust protection against corrosion. With a wide range of color and texture options available, this coating can produce glossy, matte, smooth, or textured surfaces. This sustainable and eco-friendly technique allows for the creation of thick and homogeneous surfaces in a single application.
Applications, Advantages, and Processes
Aluminum profiles produced in the electrostatic powder coating facility are used in exterior building components such as door and window frames, as well as façade cladding for modern architectural structures. In the automotive sector, aluminum rims, engine components, and other parts are favored. Due to their lightweight, durable, and aesthetically pleasing properties, these profiles are also utilized in the furniture, white goods, and electronics industries. These materials stand out for their low production costs, rapid and efficient manufacturing processes, high coating quality, long-lasting protection, and recyclability.
The electrostatic powder coating process consists of the following stages:
Surface Preparation: The aluminum surfaces are cleaned, removing oils and dirt to achieve a flawless finish.
Chemical Cleaning: Solvents, phosphating, and chromating processes are applied through chemical cleaning methods.
Mechanical Cleaning: Sanding or blasting is used to eliminate dirt and imperfections from the surface.
Powder Application: The powder coating is applied to the aluminum surfaces after being charged with an electrostatic gun. The electrostatic attraction aids in the even distribution of the paint across the surface.
Curing: The painted aluminum parts are cured in an oven at temperatures of 180-200°C, melting and hardening the powder coating, thereby increasing its durability.
Cooling: After curing, the parts are cooled in a controlled manner to become ready for use.
To explore the high-quality products of various colors and types designed at Mekaline Aluminum's electrostatic powder coating facility, visit our website.