HISTORY OF ALUMINUM
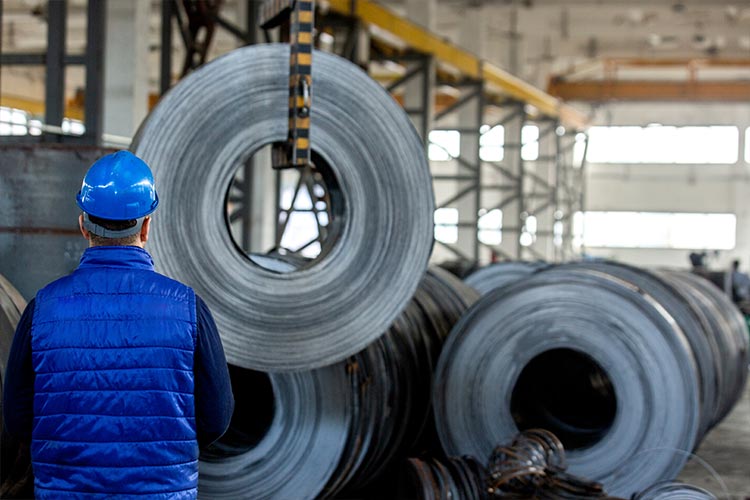
Aluminum is increasingly gaining interest across all sectors due to its numerous beneficial and effective properties. Notable for its light weight, softness, ease of processing, corrosion resistance, durability, conductivity, recyclability, cost-effectiveness, environmental friendliness, and sustainability, aluminum was initially considered a rare and expensive metal. However, advancements in production techniques have made it more affordable and widespread. Mekaline Aluminum has compiled the development processes of this strategic material from the past to the present
Aluminum drew significant attention as a primary raw material for many industrial applications by the late 19th century due to its numerous advantages. The adaptation of the "electrolytic method" for industrial aluminum production in 1886 marked a groundbreaking development in the field.
In the 20th century, aluminum became a critical material, especially in fields such as construction, aerospace, automotive, and packaging. During World War II (1939-1945), it was extensively used in aircraft production, electrical cables, and home decor products. This increased demand significantly for aluminum.
What Are the Development Stages of Aluminum?
The discovery of aluminum, which forms the basis for many technological and industrial advancements today, dates back to the 18th century. Here are some key milestones that shed light on the history of aluminum:
- In 1754, German chemist Andreas Sigismund Marggraf (1709-1782) was the first to obtain alumina (aluminum oxide) from the mineral alum (potassium aluminum sulfate). However, pure aluminum metal had not yet been isolated.
- In 1807, English chemist, physicist, and inventor Humphry Davy (1778-1829) identified aluminum as a component of an iron alloy. Davy aimed to obtain aluminum from a mixture of alumina and potassium through electrolysis and proposed the name "aluminum" for the element.
- In 1821, bauxite ore, the raw material for aluminum, was discovered in the south of France.
- In 1825, pure aluminum was first produced by Danish physicist and chemist Hans Christian Ørsted (1777-1851). Ørsted reduced aluminum chloride using potassium amalgam and isolated the metallic aluminum.
- In 1827, German chemist Friedrich Wöhler (1800-1882) advanced Ørsted's work by producing larger quantities of purer aluminum. Wöhler's method was based on the reduction of aluminum chloride and potassium.
- In 1845, German chemist Friedrich Wöhler produced a sufficient quantity of aluminum to analyze its density.
- In 1852, German chemist Robert Wilhelm Bunsen (1811-1899) further developed Humphry Davy's method, achieving the separation of metallic aluminum through an electrolytic process.
- In 1854, French chemist Henri Etienne Sainte-Claire Deville (1818-1883) developed the first chemically viable process for aluminum production. This method, which allowed for large-scale aluminum production, was built upon Friedrich Wöhler's work. Deville reduced aluminum chloride using sodium, thereby producing larger quantities of pure aluminum. This invention laid the foundations for the aluminum industry, reducing production costs and paving the way for broader use of the element.
- The year 1886 marked a turning point in modern aluminum production. In this year, the large-scale production of aluminum became possible through the "Hall-Héroult" process, which was independently discovered almost simultaneously by American chemist Charles Martin Hall (1863-1914) and French scientist Paul Héroult (1863-1914). This breakthrough involved melting aluminum oxide in cryolite and electrolyzing it to obtain aluminum. This process led to a significant increase in aluminum production and laid the foundation for the formation of competitive aluminum prices in the market. The Hall-Héroult process is still used in aluminum production today.
What Is the Bayer Process?
- It is possible to obtain pure aluminum from bauxite ore using various techniques. Among these, the most widely used is the Bayer Process, developed by Austrian chemist Carl Josef Bayer (1847-1904). This process involves first extracting alumina (aluminum oxide, Al₂O₃) from bauxite ore, followed by the production of pure aluminum through electrolytic reduction.
- Today, aluminum is also obtained from the recycling of secondary aluminum scrap metal. Due to energy savings and sustainable environmental practices, the demand for secondary aluminum production is steadily increasing.